Introduction
Diesel generators are a crucial component of various industries and applications where a reliable source of backup power is required. These generators are known for their robustness, durability, and ability to provide a consistent power supply even in the most demanding conditions. However, in order to ensure optimal performance and efficiency, it is essential to conduct regular performance analysis of diesel generators. This article will explore the importance of performance analysis for diesel generators, the key parameters to consider, and the methods used for analyzing and optimizing their performance.
Importance of Performance Analysis
Performance analysis of diesel generators is vital for several reasons. Firstly, it helps in assessing the overall health and condition of the generator, identifying any potential issues or malfunctions that could affect its performance. By monitoring key parameters such as fuel consumption, load capacity, and operating temperature, operators can detect anomalies early on and take corrective actions to prevent breakdowns and downtime.
Secondly, performance analysis allows for the optimization of fuel efficiency and operational costs. By tracking fuel consumption and efficiency metrics, operators can identify opportunities to reduce fuel wastage and improve overall efficiency, resulting in cost savings and environmental benefits.
Furthermore, performance analysis helps in ensuring compliance with regulatory standards and industry best practices. 200kw diesel generator for remote infrastructure projects monitoring and analysis can help organizations demonstrate adherence to safety and environmental regulations, as well as meet industry standards for reliability and performance.
Key Parameters for Performance Analysis
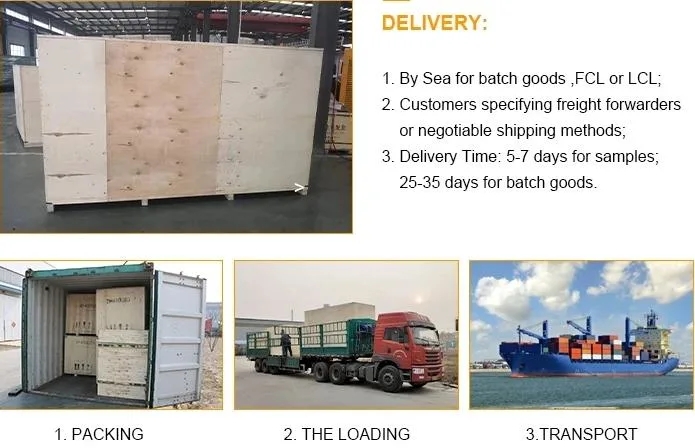
Several key parameters need to be monitored and analyzed to assess the performance of a diesel generator effectively. These parameters include:
1. Fuel Consumption: Monitoring fuel consumption is essential for evaluating the efficiency of a diesel generator. By tracking fuel usage over time and comparing it to the expected consumption rate, operators can identify any inefficiencies or abnormalities that may indicate a problem with the generator.
2. Load Capacity: The load capacity of a diesel generator refers to the maximum amount of power it can deliver under varying loads. Monitoring the load capacity helps in ensuring that the generator can meet the power demands of the connected equipment without overloading or underperforming.
3. Operating Temperature: The operating temperature of a diesel generator is a critical parameter that indicates the efficiency and health of the engine. High operating temperatures can lead to overheating and engine damage, while low temperatures may affect the combustion process and overall performance.
4. Voltage and Frequency: Voltage and frequency output are crucial parameters that determine the quality of power delivered by a diesel generator. Monitoring these parameters helps in ensuring stable and reliable power supply to connected equipment and preventing damage from voltage fluctuations.
Methods for Performance Analysis
There are several methods and tools available for analyzing the performance of diesel generators. These methods range from simple visual inspections to advanced data logging and analytics techniques. Some of the common methods for performance analysis include:
1. Visual Inspections: Regular visual inspections of the diesel generator can provide valuable insights into its overall condition and performance. Operators can check for signs of wear and tear, leaks, loose connections, and other visible issues that may affect performance.
2. Fuel Consumption Monitoring: Installing fuel flow meters or using fuel monitoring software can help in tracking fuel consumption and identifying any deviations from the expected consumption rate. This data can be used to optimize fuel efficiency and detect fuel-related issues.
3. Load Testing: Conducting load tests on the diesel generator under varying load conditions can help in assessing its performance and capacity. By simulating different load scenarios, operators can determine the generator's ability to handle peak loads and identify any limitations or inefficiencies.
4. Remote Monitoring Systems: Implementing remote monitoring systems that collect real-time data on key parameters such as fuel consumption, temperature, voltage, and frequency can provide operators with continuous insights into the generator's performance. These systems enable proactive maintenance and troubleshooting, leading to improved reliability and uptime.
5. Data Analytics: Utilizing data analytics tools and software to analyze performance data collected from the generator can help in identifying trends, patterns, and anomalies that may indicate potential issues or areas for improvement. By analyzing historical data and performance metrics, operators can make informed decisions to optimize the generator's performance.
Conclusion
Performance analysis of diesel generators is essential for ensuring reliable and efficient power generation in various applications. By monitoring key parameters such as fuel consumption, load capacity, operating temperature, and voltage output, operators can assess the performance of the generator and identify opportunities for optimization. Utilizing methods such as visual inspections, fuel consumption monitoring, load testing, remote monitoring systems, and data analytics can help in maintaining the health and efficiency of diesel generators, ultimately leading to cost savings, reliability, and compliance with industry standards. Regular performance analysis is key to maximizing the lifespan and performance of diesel generators and ensuring uninterrupted power supply when needed.